模具维修报告后的处理步骤:确保生产效率与产品质量的双重提升
在工业生产中,模具作为关键的生产工具,其性能直接影响着产品质量和生产效率。当模具发出维修报告时,如何科学、高效地处理这些问题,成为保障生产线稳定运行的重要环节。本文将针对模具维修报告后的处理策略,从分析报告内容、制定维修计划、实施维修措施以及后续跟踪等方面进行详细阐述。
一、分析维修报告,明确问题根源
对于模具维修报告,我们必须进行详细的分析。报告通常包括以下几个方面:
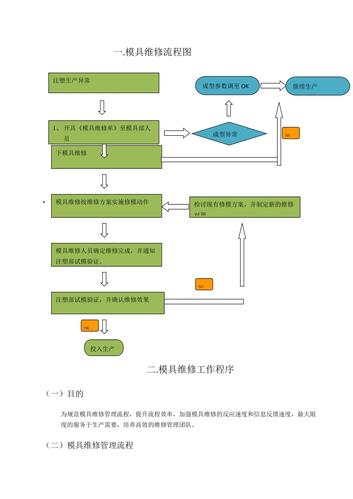
1. 故障现象:描述模具在运行过程中出现的异常情况,如磨损、变形、断裂等。
2. 故障原因:分析故障产生的原因,可能是材料问题、设计缺陷、操作不当等。
3. 维修建议:提出针对故障的维修方案,包括更换零部件、调整工艺参数等。
在分析报告时,我们要重点关注以下几个方面:
- 故障现象的严重程度:判断故障是否影响生产,是否需要立即停止生产进行维修。
- 故障原因的复杂性:分析故障产生的原因,是否需要专业技术人员进行处理。
- 维修建议的可行性:评估维修方案的可行性,包括维修成本、维修周期等。
二、制定维修计划,确保生产有序进行
在明确故障原因后,我们需要制定详细的维修计划,以确保生产有序进行。以下是一些关键步骤:
1. 评估维修成本:根据维修方案,评估维修所需的材料、人力、设备等成本。
2. 制定维修时间表:合理安排维修时间,尽量减少对生产的影响。
3. 通知相关部门:将维修计划通知生产、采购、质量等部门,确保各部门协同配合。
三、实施维修措施,确保维修质量
在制定好维修计划后,我们需要严格按照计划实施维修措施。以下是一些关键点:
1. 选用优质材料:确保维修使用的材料符合标准,保证维修后的模具性能。
2. 严格操作规程:按照维修方案,严格按照操作规程进行维修,避免人为因素导致的问题。
3. 加强质量控制:在维修过程中,加强对关键环节的质量控制,确保维修质量。
四、跟踪维修效果,持续改进
维修完成后,我们需要对维修效果进行跟踪,以确保模具恢复正常运行。以下是一些关键措施:
1. 测试模具性能:对维修后的模具进行性能测试,验证维修效果。
2. 收集反馈意见:收集生产一线的反馈意见,了解模具在实际生产中的表现。
3. 持续改进:根据测试结果和反馈意见,对模具进行持续改进,提高其性能和可靠性。
模具维修报告后的处理是一个系统工程,需要我们认真分析报告内容,制定合理的维修计划,严格按照计划实施维修措施,并持续跟踪维修效果。只有这样,我们才能确保生产线的稳定运行,提高产品质量和生产效率。
正如美国质量管理专家戴明所说:“持续改进是质量管理的基本原则。”在模具维修过程中,我们要始终秉持这一原则,不断优化维修流程,提高维修质量,为我国制造业的持续发展贡献力量。